Businesses thrive and fail depending on their quality control process. Every good company wants to operate at peak capacity, offering the best products and service possible in the most cost-effective and efficient way. This leads to greater customer satisfaction and better profits. The components to achieve this exist in a delicate ecosystem, and upsetting the balance with inefficiency, waste, or poor-quality products or services leads to the entire system falling apart. Quality control ensures this doesn’t happen. How? Through a constantly recurring process that pinpoints issues, rectifies problems, and raises the bar for the quality standard. To better understand how the quality control process works, it can be broken down into six crucial components.
Want to streamline inventory management? – Download our checklist!
6 Steps of the Quality Control Process
1. Define Controls
Controls are the standard that everything else is compared to. No matter the batch number for the item being produced, there will always be a series of controls that represent the ideal quality of the product and the process to produce it. Therefore, it’s vital that controls are thoroughly documented in a measurable way. There should be no misinterpretation of which guidelines need to be met and expectations should be understood before development or production even begins.
2. Test
Even if everything was completed in accordance with the control sets, testing is still needed to ensure no flaws went undetected. Testing involves meticulously combing over everything. Without rigorous testing, mistakes can be left unchecked, leading to loss in product quality.
3. Analyze Variance
Variance refers to anything measurable that appears during testing that doesn’t align with the control set. Ideally, no variances would be detected during testing. However, in the event that variance is detected, it needs to be analyzed in-depth and accurately documented so a proper assessment can be made.
4. Define Limits and Compare
At this point, the variances will be checked if they are within the defined tolerance levels, the statistical limits that the quality must reach. If the variances are within the established tolerance levels, then no further action is needed and the quality control process can return to step one.
5. Take Corrective Action
Should the variance exceed the tolerance level, corrective action must be taken. Even if the amount surpassed is minimal, the issue must still be addressed. Letting things slide can be a slippery slope that leads to increasingly large tolerance levels and accepting poorer quality products. There are a few ways to course-correct significant variances: the parts can be sent back for improvements or the whole batch can be rejected entirely. Either way, the control process would be repeated to ensure the customer doesn’t receive inferior products.
6. Evaluate
To guarantee authenticity, procedures need to be implemented so variances do not repeat. Once data and feedback are considered, the production process can evolve to create quality products at a more consistent rate with less waste. After this is accomplished, the entire quality control process repeats itself. This process of constantly repeating and evolving is why product quality is continuously improving.
Always Repeating. Always Improving.
Quality is never stagnant. There will always be efficiencies to be improved, waste to be reduced, and customers to continue satisfying. Repeating the quality control process is how these improvements are made. At Winn, we are constantly taking strides to raise the bar, because when it comes to quality machining, we produce excellence you can count on.
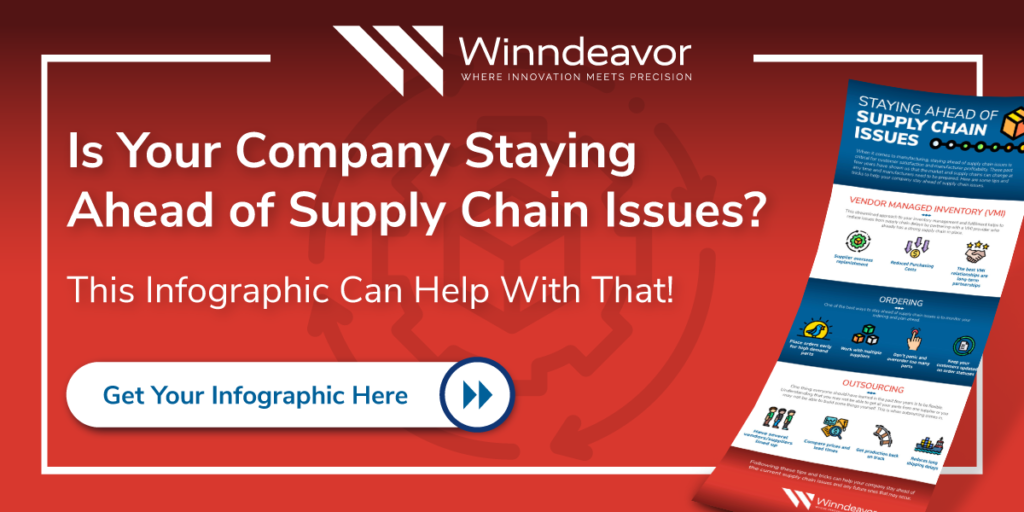