When it comes to your machined projects, you may not be using a vendor-managed inventory (VMI). If that is the case, you likely find yourself ordering parts as you need them, paying full-price for short-run orders, and risking overstock. Honestly, we think that’s a shame. Let’s talk about vendor-managed inventories: what they are and how can you go about choosing a VMI partner?
Click Here to Download our Guide to 5-Axis Machining
Vendor managed inventory is a streamlined approach to your inventory management and fulfillment. The supplier takes charge of replenishment, allowing them to adjust inventory proactively to customer demand. This improves responsiveness to seasonal changes, promotions, or initiatives you may run. Because the supplier controls inventory, they can be more efficient and informed as the ordering process is based on more accurate data; this reduces the need for expensive, last-minute orders, the total number of orders, and the cost of returns for product replacement. Customers also benefit from reduced purchasing costs simply because the vendor receives and uses that data rather than purchase orders, so the purchasing department doesn’t have to spend as much time calculating and producing purchase orders.
Another benefit of the VMI model is that the vendor is responsible for supplying the customer when items are needed. This leads to the removal of safety stock, lower inventory levels, and reduced purchasing-related administrative costs.
The goal of a VMI is to align business objectives and streamline supply chain operations for both suppliers and customers: improving inventory turns, improving service, and increasing sales.
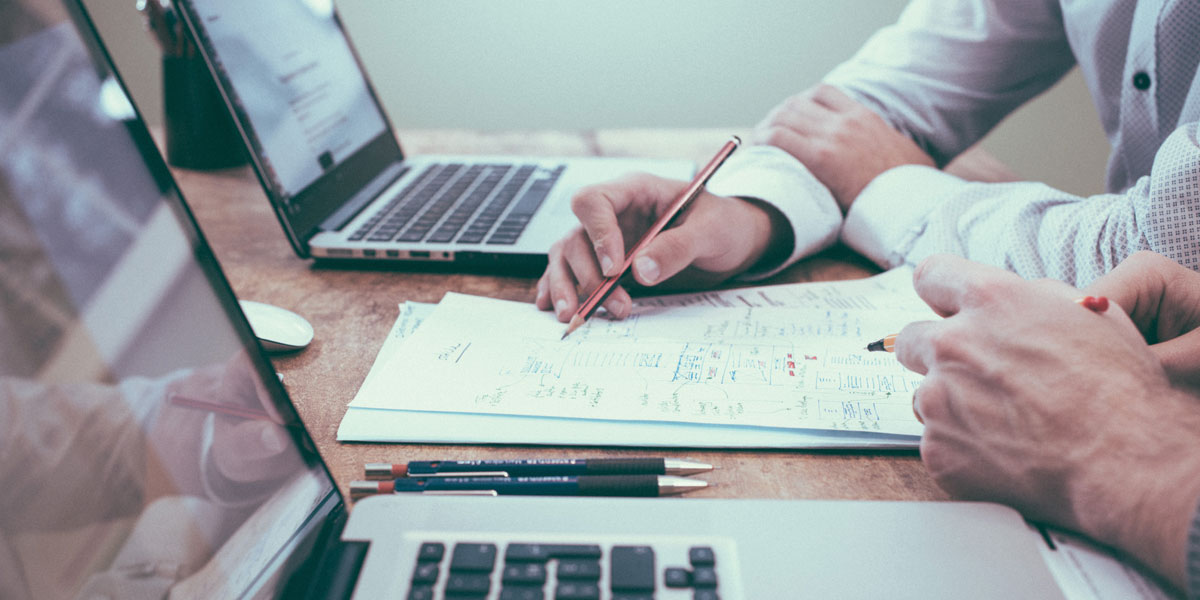
A good VMI provider will meet with their client to create a custom-built VMI program that best suits their needs.
What should you look for when choosing a VMI? The best VMI relationships are partnerships, so keep the criteria of experience, flexibility, and foresight in mind.
Experienced VMI providers have a successful track record assessing, developing, and implementing solutions for your organization. They have a deep understanding of your market, your market demand, and your products. They also need to have a strong supply chain, which allows for faster response time in cases of unforeseen demand or market volatility. Ask for documented, proven, high-quality results.
Bad VMI providers offer up canned, cookie-cutter programs recycled from a previous customer. Good partners will start by getting to know you and your organization: walking-through your plant or warehouse–taking the time to speak to you and anyone else who can provide insights in creating and implementing your custom-built program.
Finally, the best VMI providers use their experience and your custom plan to forecast next steps and to improve your plan using smart, data-driven decision-making. Top-tier VMI partners report on business reviews and analysis, market trends, inventory consumption trends and patterns, and data-driven recommendations for improvements.
Vendor-managed inventory partnerships offer many benefits from cost and inventory perspectives, which helps you better serve your customers needs. We believe that VMI solutions will help you and your company be the best that you can be, and we want to help you get there.