Production costs are on the rise across many industries. Manufacturers are struggling to remain competitive in the current market. Many have started to look for ways to increase productivity and efficiency across their systems. One technique that manufacturers are using is called Lean Manufacturing. Let’s look at the 5 Lean Manufacturing Principles that are used to cut costs and increase efficiency.
Find out How to Implement a VMI Strategy
What is Lean Manufacturing?
Lean Manufacturing focuses on minimizing waste and removing unneeded steps that are not necessary to the production process. Reducing waste helps lower production time, improve product quality, and reduce overall production costs.
5 Lean Manufacturing Principles
There are 5 principles to lean manufacturing. They are defining value, mapping the value stream, creating flow, using a pull system, and pursuing perfection.
1. Defining Value
- Lean manufacturing aims to add value for the end customer. When defining value, look at what the customer wants, needs, and what they are willing to pay. Ways to do this include interviews, surveys, and researching demographic information.
2. Mapping the Value Stream
- This step works by taking the customer’s values as a reference point and finding areas that follow these values. Anything that does add value to the end customer is considered wasteful in this process. Two types of waste come from this process: necessary and unnecessary. Neither add value but the necessary waste can only be reduced while the unnecessary waste should be removed from the process.
3. Creating Flow
- The next step in the lean manufacturing process is to ensure that the flow of the process remains smooth after the waste has been removed or reduced. Some steps in production may need to be reworked during this step to ensure that value is still being added for the end customer.
4. Using a Pull System
- This step works to establish a pull-based system. A pull system works to reduce waste by minimizing inventory and work in process items. This allows for a smoother more efficient workflow while ensuring that products are delivered on time.
5. Pursuing Perfection
- Lean manufacturing does not end once the waste is eliminated from the production process. Pursuing perfection means continuous work towards improving production and adding value to the end customer. Lean manufacturing should become a part of the company culture that all employees strive to work towards.
Benefits of Lean Manufacturing
There are many benefits to the lean manufacturing process. Some of these benefits include:
- Waste minimization
- Cost reduction
- Streamlined process
- Quality improvement
- Meeting deadlines
If your company is looking for a way to reduce costs and increase productivity, then lean manufacturing may be an option for you to consider. Lean manufacturing reduces waste and costs while also adding value to the end customer. To learn more about lean manufacturing principles contact Winndeavor today!
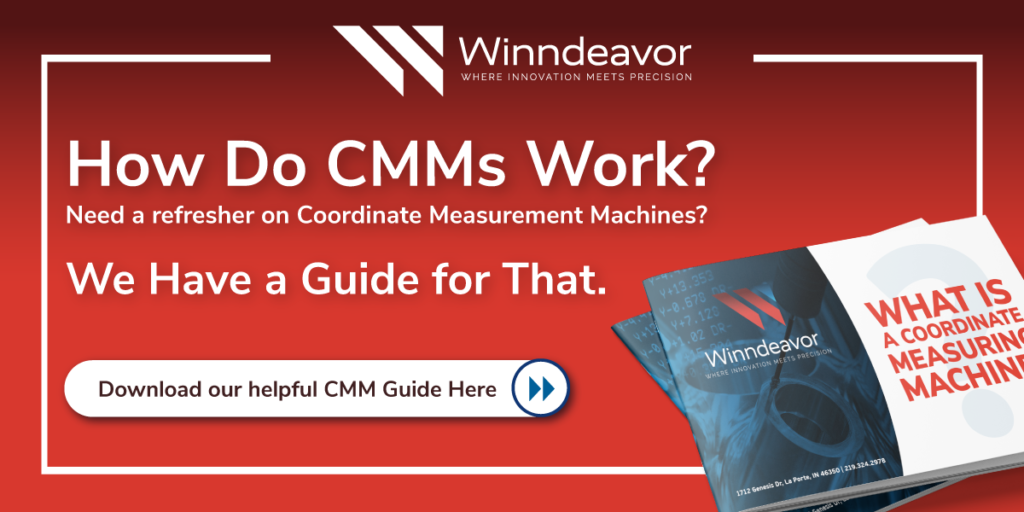