One of our favorite aspects of machining is how many processes are out there for manufacturers and enthusiasts to master. We’ve discussed a number of these processes in the past and in this post we’re going to take a closer look at one that always garners a ton of interest: hard turning.
Find out How to Implement a VMI Strategy
Let’s begin with a simple definition of what hard turning is. Hard turning is the process of single-point cutting workpieces with hardness between 58 and 70 HRC. The process started to develop in the early 1990s because of the availability of new tool materials and the increased capabilities and rigidity of the turning machines themselves. In tandem, the result of these developments was a truly viable alternative to grinding for finishing operations. This begs the question: how does hard turning compare to the more traditional means of finishing? As both processes can be used as a means of finishing, they are often put in competition with each other.
First, not just any lathe can be used. The machine must be rigid enough to withstand the forces being exerted upon it by the hard turning process. This is one of the key reasons for its increased popularity: machine shops don’t need to use up floor space for machines that exclusively grind parts. Lathes can be productive even when they’re not hard turning because they’re doing other things. This increases the shop’s overall productivity and economy.
The second advantage of hard turning is that is shares the fundamentals with “soft turning.” While every machining process has its inherent complexities, grinding requires very specified knowledge and experience that many machinists don’t have; hard turning requires only adjustments to what the machinists already know to learn the process.
Here are ten ways hard turning reduces cost:
- The same machines can hard turn and “soft turn.”
- Requires less floor space.
- Lower overall investment.
- Greater metal removal rate.
- Turn along complex contours.
- Perform multiple operations in one setup.
- Low micro finishes.
- Easier to configure changes.
- Lower cost of tooling inventory.
- Easier on waste management.
Beyond the economic benefits, what about the process itself? Hard turning is ideal for complex workpieces which require both internal and external machining. Complex geometries can usually be accurately generated by CNC slide positioning and cutting with a CBN insert (though these inserts do tend to be rather pricey). Additionally, operations can often be completed in one part clamping, so it’s much easier to set up and change over. Grinding, on the other hand, every individual contour needs to be generated by a specifically formed grinding wheel which needs to be redressed at regular intervals. Hard turning is especially well-suited to small and medium-sized production runs over a wide variety of workpiece types. So, as we can see, the hard turning process can yield very tangible benefits to your machined parts and your bottom line. If you’re looking to incorporate it into your finishing, we want to help you.
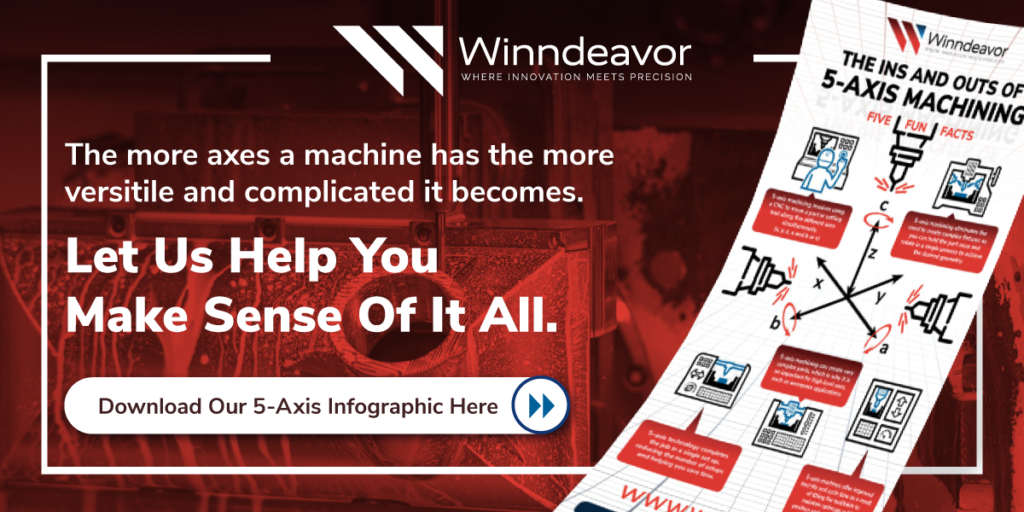